A shell and tube heat exchanger is a cornerstone of many production operations, designed to last for years under tough conditions. However, certain processes, especially those involving high fluid velocities, can lead to challenges like corrosion, erosion, and excessive vibrations. These issues not only impact the machine’s performance but can also reduce its lifespan, as vibration can cause tubes to pull out, leading to cross-contamination and damage to both the tubes and the shell.
To mitigate these risks, the Tubular Exchanger Manufacturers Association (TEMA) advises that when dynamic pressure (rho*v2) exceeds 1,500 in certain high-velocity situations, an impingement plate should be installed. These plates help reduce erosion and vibration by diffusing the high-energy fluid. However, they come with their own drawbacks, such as increasing the shell diameter or creating vibrations themselves. Therefore, careful consideration is needed before making modifications to the heat exchanger.
The Role of Impingement Devices in Steam Heating Systems
In steam heating applications, the use of impingement devices can significantly improve the efficiency and longevity of the heat exchanger. Steam heating systems are vital for various industrial processes, such as cleaning, sanitation, and product heating, and rely on maintaining precise temperature and pressure levels. Shell and tube heat exchangers are central to these systems, ensuring effective heat exchange between process liquids and steam.
Impingement devices help regulate the heat exchange process by increasing turbulence, reducing stagnation, and limiting corrosion. These devices keep the steam moving, particularly near the shell-side inlet, which enhances heat distribution and reduces the risk of vibration.
Exploring Virtual Testing and Other Solutions
Determining the best solution for high-velocity processes can be challenging. While impingement plates are effective, they may not always be the ideal solution. Using computer simulations, such as HTRI software, manufacturers can predict how different equipment will affect heat exchanger performance. These simulations use complex models to analyze fluid flow and allow engineers to explore other methods to reduce erosion and vibration risks.
Beyond impingement plates, other protective devices can be used to reduce vibration and prevent erosion. Options like annular distributors, impingement rods, and different baffle configurations (such as double-segmental) can save space and cost while addressing thermal expansion issues. In some cases, longer shells or U-tube designs offer further protection, preventing tube pullout or shell damage.
Types of Impingement Devices
At Enerquip, a variety of impingement devices are available to improve heat exchanger performance. The choice of device depends on factors such as fluid properties, velocity, and system pressure drops. Here are some common options:
• Baffles: These are installed perpendicular to fluid flow to increase turbulence and change the fluid’s direction, improving heat distribution.
• Annular Distributor (also called a steam bustle or vapor belt): This device ensures even fluid distribution over the tubes, preventing hot and cold spots.
• Twisted Tubes: Shaped like a corkscrew, these tubes disrupt fluid flow to ensure even heat distribution.
Maximize Efficiency with Enerquip
Choosing the right impingement device is essential for ensuring the longevity and efficiency of your heat exchanger, whether for industrial or sanitary applications. At Enerquip, we specialize in steam heating solutions and can help you determine the best methods to reduce erosion, vibration, and ensure efficient heat exchange.
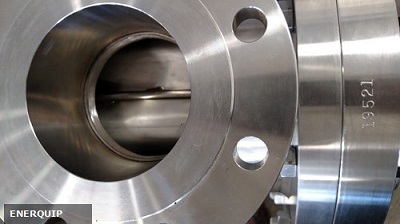