Stepper motors are commonly used to translate motion from rotary to linear. Selecting the right combination of electrical and mechanical components is complicated by the various options for precision positioning systems. This brief will review key criteria for successful stepper linear actuator specification and highlight the benefits of correct actuator and application pairings.
An integrated stepper linear actuator system combines a hybrid stepper motor with a lead screw or nut attached as an integral part of the motor shaft. This integrated electromechanical solution offers precise positioning for many applications at an affordable price.
The integrated stepper linear actuator design provides optimal performance in terms of linear force and speed, load rating, system efficiency and reliability. Fewer mechanical components mean lower costs and greater system accuracy. This integrated solution is also compact in size to allow for smaller equipment footprints.
1. Know the stepper linear actuator types
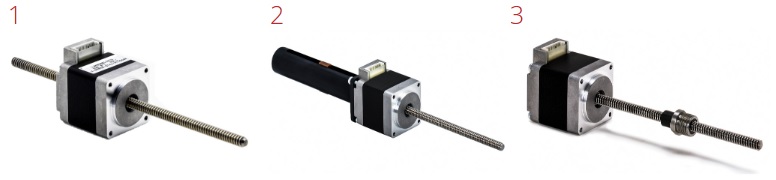
Figure 1. From left: Standard linear actuator; guided linear actuator; and leadscrew motor.
The standard linear actuator (non-captive, internal nut) is configured with the leadscrew nut integral to the stepper motor rotating shaft, inside the motor. The leadscrew end connects to the moving device while the device provides the mechanical support to prevent rotation of the leadscrew. As the stepper motor rotates, the leadscrew translates linearly through the body of the motor, pulling or pushing the connected device with precision motion. A typical application includes a precision metering or dispensing pump that provides mechanical support and anti-rotation of the leadscrew.
The guided linear actuator (captive, internal nut) is similar in functionality to the non-captive linear actuator but uses the stepper motor to provide mechanical support and prevent rotation of the leadscrew. In this configuration, leadscrew stroke length is limited based on the size/length of the motor support mechanism. A typical application includes a precision metering or dispensing pump that does not provide mechanical support and anti-rotation of the leadscrew.
The leadscrew motor (external nut) features the leadscrew as an integral part of the stepper motor rotating shaft and the nut is external to the motor. The connected load is mounted to the external nut and must prevent the nut from rotating. The stepper motor rotates the leadscrew, which causes the external nut (and the connected load) to move in a precise linear motion. A typical application includes a positioning table, sample handling system or pick-and-place system that requires precise positioning.
Notably, anti-backlash nuts can be applied to any of the above configurations to provide a higher level of precision.
2. Understand application needs
Figure 2. The ElectroCraft AxialPower Enhanced Series APES17.
Based on the application’s required operating conditions in terms of force, speed and precision, users can easily select the optimal solution from the manufacturer’s published performance curves. Things to consider include:
-
Frame size (typically NEMA sizes) — Each larger frame size provides higher levels of output force and load carrying capability.
-
Force — Maximum force is determined by motor frame size, motor stack length and leadscrew thread lead.
-
Precision — Positioning accuracy is determined by a stepper motor minimum step angle and leadscrew thread lead.
-
Speed — Speed range is determined by the stepper motor winding current and leadscrew thread lead.
3. Select a stepper drive that is compatible with the linear actuator
Stepper linear actuators are controlled with stepper motor drive electronics. These stepper drives range from simple open or closed loop control using digital step and direction inputs to more sophisticated motion control capabilities using a built-in motion program that can be controlled over a network such as CAN bus. Stepper drive hardware can be stand-alone or integrated with the linear actuator motor assembly.
4. Consider the wide application capabilities
Applications for integrated stepper linear actuators include medical equipment (precision pumps used for injection or infusion), imaging equipment (CT scans and MRIs) and diagnostic equipment (blood analyzers). For lab automation, these integrated systems are found in precision pumps used for metering and dispensing, gas and liquid chromatography systems, mass spectrometry systems and pick-and-place systems used for test tube handling.
Electronic assembly operations use integrated stepper linear actuators for precision positioning systems, material handling and pick-and-place systems, as well as assembly and test equipment systems. Semiconductor processing equipment incorporates integrated systems into microfluidics, precision dispensing pumps and precision positioning systems.
5. Check with the experts
Manufacturers have the engineering experience and expertise from decades of facilitating customers with integrated stepper linear actuator products. They often provide innovative solutions for a wide range of applications across all major market segments. Plus, they are able to suggest custom and semi-custom solutions suited for a specific case. Contact ElectroCraft today for expert guidance.