Watching an automated guided vehicle (AGV) system in action is to witness an engineering marvel: The AGV, with a payload worth several millions, must be controlled to within millimeters (5-millimeter accuracy). The coordination of the AGV systems presents a challenge.
AGV systems represent only one of 15 advanced automation system product lines, which Fori Automation supplies to the aviation, automotive, and defense industries. Founded in 1984 outside of Detroit, the company now has set up facilities worldwide to serve customers around the globe.
Among automation systems, AGV systems pose some of the greatest and most complex challenges with regard to operation, control, and safety. That is because they are specifically designed for moving large and expensive payloads and tooling through the production floor.
Wireless Communication System as Solution
The development of a reliable, secure, and safe wireless communication system for its multipurpose AGV systems is a prerequisite for a smooth operation.
AGV systems from Fori Automation are massive, 25-ton rectangular-shaped metal boxes about 40 feet in length and 15 feet in width. Engineered polyurethane swivel casters support the AGV and tooling weight, minimizing the floor loading requirement, and allowing for multidirectional AGV motion. Four Hall-effect sensors ensure proper AGV positioning and a highly accurate guidance.
The most common method to provide AGV systems with tracked guidance is to lay a magnetic bar in a narrow trench,which has been cut into the plant’s concrete floor, and to cover it with epoxy.
An orchestrated Performance
According to Greg Stegner, project engineer for control systems at Fori Automation, synchronizing the control and operation of a large number of AGV systems simultaneously becomes quite complicated. “The AGV systems typically move through large plant spaces performing different tasks,” says Stegner. “The loaded AGV systems are in constant communication with other plant systems; consequently, this communication must never be interrupted.”
To choreograph this complex task, operators had been using a mix of tethered and wireless human machine interfaces (HMIs). “In past, tethered HMIs worked fine, but the cords had to be managed well,” explains Stegner. “But then the cords still failed or they broke; that is why we needed an all-wireless HMI that was easy to learn and use, as well as secure, reliable, and uninterruptible.”
According to Stegner, the time had come to consolidate the communication and control on a single wireless local area network (WLAN). He and his team chose Siemens to supply that network for two reasons. They not only valued the innovative technology and high quality of the components, but also knew that the product portfolio included everything they needed. “We did not want to deal with components from different suppliers,” states Stegner. “That would have caused all kinds of system integration issues.”
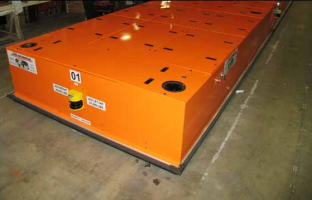
Ensuring Integrity and Security
Stegner and his team decided to employ a PROFINET-based wireless Industrial Ethernet network in the 5 GHz frequency band with PROFIsafe protocols using the distributed I/O SIMATIC ET 200S and SCALANCE components. The 5 GHz frequency band with nine channels provides greater security than the 2.4 GHz frequency band with only three channels.
Although other Industrial Ethernet protocols are available, PROFINET is the leading global standard with almost five million nodes in operation. PROFINET uses the TCP/IP Ethernet standard with extensions from special industrial protocols that enable a deterministic real-time communication. This was critical to fulfill the requirement of an uninterruptible wireless communication.
For added safety, the application was implemented with Siemens PROFIsafe – the first communication standard in accordance with the IEC 61508 safety requirements. This enables the transmission of both standard control data and safety-related data on a single channel.
Three-layered Architecture
The solution’s overarching architecture is comprised of three layers:
(1) The AGV system control layer – including onboard controls and wireless HMI operating console;
(2) The layer for the coordination of the plant (“traffic cop”) as well as
(3) The IT infrastructure and IT systems of the plant – including manufacturing execution system (MES) and enterprise resource planning (ERP) software, such as SAP.
To control the AGV system’s onboard safety functions, Fori Automation uses the Siemens interface module IM151-8F PN/DP with failsafe SIL-3 CPU functionality for the distributed I/O SIMATIC ET 200S. The guidance and positioning sensors of the AGV system are connected to its servo drives via SIRIUS contactors. To control the AGV system, operators use the portable, wireless HMI device SIMATIC Mobile Panel 277F-IWLAN.
Plant-wide wireless Coverage
Both safety and control devices communicate via PROFINET with a SCALANCE X switch that is connected to a wireless SCALANCE W client. This client onboard the AGV communicates via the 5 GHz band with permanently mounted SCALANCE W access points (APs). The APs are IP65-rated to withstand the harshest of industrial environments. The APs are distributed throughout the plant to obtain maximum range with overlapping radio signals.
In the past, AGV systems were usually guided by a fixed induction loop. With PROFINET, a continuous communication between the AGV system and the plant’s master PLC is possible every step of the way. As a result, a much greater freedom of movement and positioning flexibility of the travel circuits are achieved.
Industrial Point Coordination Function (iPCF)
Siemens iPCF has been developed for wireless industrial realtime applications. When using iPCF, each SCALANCE AP functions as a coordinator for the data traffic and polls clients for I/O data in short cycles. This lets standard data – such as transport orders, status messages, and failsafe communication – run in parallel on the same connection. All wireless communication has to be uninterruptible.
According to Stegner, it was easy to set up the PROFINET network. “You open a browser and follow the prompts from several wizards guiding you through the process. All WLAN and security settings are provided, and the iPCF functionality is set up.” With the Siemens PROFINET-based wireless solution, Fori Automation can now deploy up to 50 AGVs in a plant via iDevice; almost three times as many as before.
Improved Safety and less Time required
By eliminating tethered HMI controls, operating the AGV systems has become much easier. The tight integration of the vehicle’s onboard safety PLC as well as the extended WLAN integration with controls and the operation of other AGV systems dramatically improve the plant safety. “PROFINET has also expanded our diagnostic capability,” continues Stegner.
He adds that the seamless interoperability of the Siemens components has greatly reduced the time required by Fori Automation engineers to develop, set up, and test AGV solutions. “Siemens is dedicated to open standards – for the same reason Fori Automation is,” he explains. “This allows us to better tailor more of our solutions to our customer requirements, which could not be achieved with a one-size-fits-all, universal AGV system. We can thus provide superior solutions faster and at lower prices.”