Designing modern flow control components for life science, analytical and medical applications can be a difficult task in itself, but designing them from a manufacturer’s perspective incorporates additional complexity. Bürkert Fluid Control Systems, a leading manufacturer of control and measuring systems for fluids and gases, is making its entire design and manufacturing expertise available to OEMs to help them produce more cost effective and reliable products.
Renowned for producing innovative, high quality and reliable valve and manifold technology, Bürkert designs and manufactures its entire product range, which requires extensive metal and plastic machining as well as injection moulding and 3D printing technology. Now this wealth of experience and knowledge can be used by OEMs to create solutions using the latest in design and materials technology.
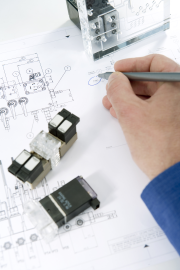
Bürkert uses an international network of Systemhaus facilities to take requests from customers and develop them into finished products locally, using a philosophy developed over 15 years which allows the company’s development engineers to pool resources and knowledge in order to solve problems at the Systemhaus design and development hubs. The whole process focuses on the clients’ requirements and how they can be delivered by the best qualified team in the most efficient way.
The first step for the team is to use their expertise to help the client understand all the available solutions and develop a design which will meet all the necessary specifications and standards as well as perform reliably and integrate with any existing infrastructure. By using 3D CAD animations or simulations combined with expert knowledge in manufacturing, materials and tool design, a firm production concept can be delivered at an early stage.
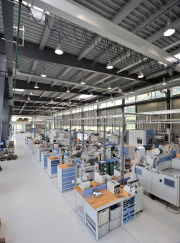
Within the Systemhaus facility it is only a short distance between the design office and the production areas, which helps in the communication of the product definition to the production engineers, who have the ability in some cases to deliver a functional model within 24 hours. The project team can deliver sample components to the client along with all the necessary local and global approvals to ensure that the design can go into production.
The facilities available within the Systemhaus include injection moulding machines and specialist tools for creating micro-fluidic valve manifolds, both of which can be used to create innovative and unique designs specifically tailored to meet the client's specifications. The designs are driven by the extensive knowledge and experience that has been accumulated over the years spent perfecting Bürkert's own products.
The ability to create original moulds using in-house machining facilities and printed circuit boards (PCBs) combined with the process and control valve technology of Bürkert, ensures that the client receives an optimised design from a single source. This process is made both effective and efficient through the appointment of a dedicated project team, whose purpose is to realise the client's design brief and to keep the client informed throughout the life of the project.
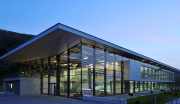
For the OEM, the end result is an integrated system, sourced through one supplier, designed to be cost effective to manufacture and to deliver reliable service. In many cases the ability of the Bürkert engineers to think 'outside the box' has enabled a new design concept to be introduced to the OEM that will simplify manufacturing and reduce overall costs.
www.burkert.co.uk